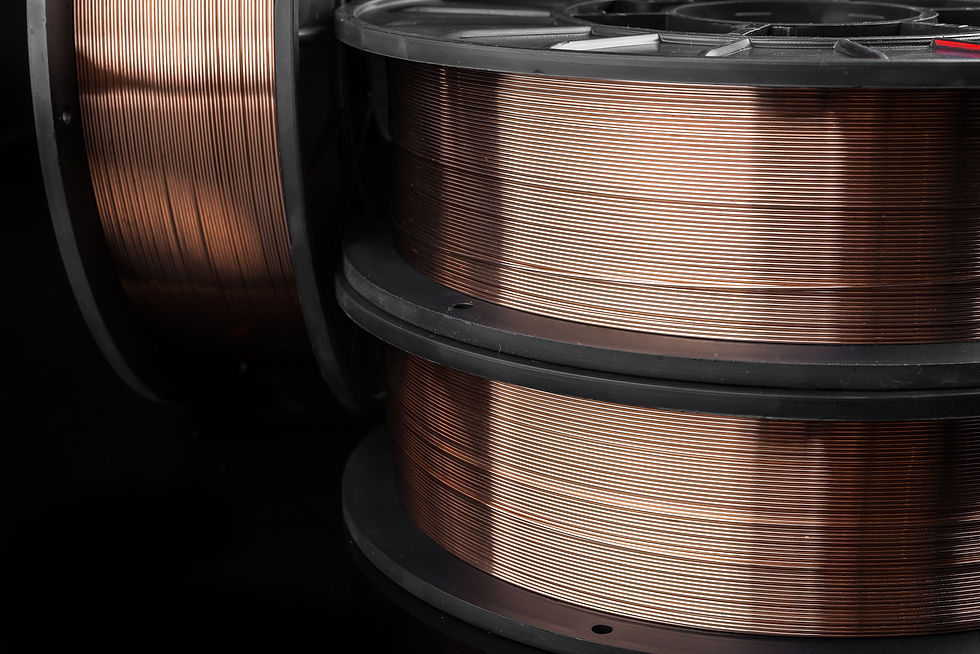
When it comes to welding, choosing the right wire is critical for the strength, quality, and durability of your welds. With so many options available, selecting the best welding wire can be a bit overwhelming, especially for Australians tackling various projects, from automotive repairs to structural steelwork. This guide will help you navigate the key factors in choosing the right welding wire for your specific needs.
1. Understand the Welding Process . How to Choose the Right Welding Wire for Your Project
Before selecting a welding wire, it’s essential to know which welding process you’ll be using. Here are the most common types and their compatible wires:
MIG Welding (Metal Inert Gas): This process uses a continuously fed wire and requires shielding gas. MIG welding is great for quick, clean welds on various metals.
TIG Welding (Tungsten Inert Gas): While TIG welding doesn’t use a wire in the same way as MIG, filler rods are often needed, and these come in various compositions.
Flux-Cored Arc Welding (FCAW): This method doesn’t require external shielding gas as the wire itself contains flux. It’s ideal for outdoor welding where wind might blow shielding gas away.
Each process has specific wire types that work best. For example, MIG welding typically uses solid wires, while FCAW uses flux-cored wires.
2. Match the Wire to the Metal
The material you are welding will dictate the type of wire you need. The most common metals include:
Mild Steel: A versatile metal, mild steel is often welded using ER70S-6 wire for MIG welding. It's popular for automotive and structural applications.
Stainless Steel: When working with stainless steel, you’ll need a wire like ER308L, which helps resist corrosion and creates strong, long-lasting welds.
Aluminium: For welding aluminium, aluminium-based wires like ER4043 or ER5356 are the go-to options. These wires are softer than steel and require careful handling.
Matching the composition of the wire to the base metal ensures better results, reduces the risk of cracking, and creates stronger welds.
3. Consider Wire Size
Welding wire comes in different thicknesses, known as diameters, and the size of the wire you choose can affect both the welding process and the outcome. The most common sizes are 0.6mm, 0.8mm, and 1.0mm.
0.6mm: Ideal for thinner materials such as sheet metal, often used in automotive work.
0.8mm: This is the most commonly used size for general-purpose welding of mild steel.
1.0mm: Suitable for heavier materials like structural steel, where deep penetration is required.
Thicker wire can carry more current and penetrate deeper into the metal, which is critical for heavy-duty applications. However, if you're working on thin metals, a smaller wire will prevent burn-through.
4. Check the Wire's Tensile Strength
The strength of the welding wire should match or exceed the strength of the base metal to ensure a durable bond. For instance, a wire marked as ER70S-6 has a tensile strength of 70,000 psi, which is generally suitable for mild steel. For structural applications in Australia, especially when dealing with construction or load-bearing projects, always choose a wire with the right tensile strength to avoid weakening the structure.
5. Shielding Gas Compatibility
Certain welding wires require specific shielding gases to produce the best results. For example:
Solid Wires (MIG): Typically used with Argon or an Argon/CO2 mix for clean welds with minimal spatter.
Flux-Cored Wires: These often don't need an external shielding gas, which is perfect for outdoor welding in windy conditions.
If you're doing general-purpose welding indoors, MIG wire with a gas mix like 75% Argon/25% CO2 can help you achieve cleaner results. For outdoor jobs, a self-shielded flux-cored wire is preferable since wind won’t affect it.
6. Look for Australian Standards Compliance
In Australia, it’s essential to ensure that the welding wire you're purchasing meets local safety and quality standards. Look for products that comply with AS/NZS 1554, which governs welding processes and consumables. Buying locally certified wire ensures you’re using materials designed to perform in Australian conditions, particularly given our unique climate and working environments.
7. Cost and Availability
Welding wire prices can vary based on the material and type. While it’s tempting to go for cheaper options, investing in high-quality wire will save you in the long run with better welds and fewer issues. Additionally, make sure the wire you choose is readily available in Australia. This ensures you can easily restock when needed without long delays.
8. Application-Specific Considerations
For Automotive Work: If you're doing panel work, especially on cars, go for a wire that’s designed for thin sheets like 0.6mm MIG wire. Stainless steel might require different wires if the vehicle has stainless components.
For Structural Welding: Larger-diameter wires and high-strength materials are essential to ensure the weld holds up under stress.
Conclusion
Selecting the right welding wire comes down to understanding your welding process, the base material, and the specific application. By focusing on these factors, you’ll ensure a strong, reliable weld every time. Whether you’re welding mild steel in the shed or working on an outdoor aluminium project, choosing the appropriate wire is critical to achieving the best results.
Key Takeaway: In Australia, always opt for certified, high-quality welding wires that match your project’s requirements, taking into account the welding method, metal type, and wire size for optimal performance.
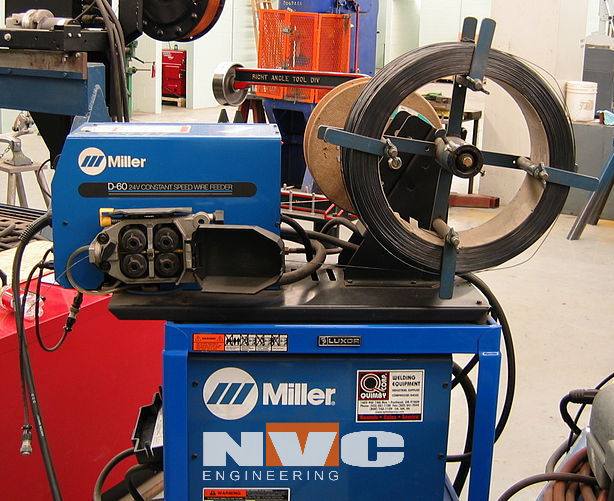
How to Choose the Right Welding Wire for Your Project
Opmerkingen