
Weld sizes and measurements are critical components in any welding project, ensuring the strength, safety, and stability of the structure. In structural welding, both the size of the weld and its throat thickness directly impact the load-bearing capacity of the joint. Accurate weld sizes and correct measurements are necessary to meet industry standards and maintain the integrity of the structure.
This guide will explain the various aspects of weld sizes, including fillet welds, groove welds, and how to properly measure welds to ensure compliance with the required specifications.
Key Terms in Weld Measurements
Before we dive into specific weld sizes, it’s essential to understand the key terms used in weld measurement.
1. Throat Thickness
The throat thickness is the shortest distance from the root of the weld to the face of the weld. It plays a major role in the strength of the weld joint.
2. Leg Size (Fillet Welds)
In fillet welds, the leg size refers to the distance from the root of the weld (where the two pieces of metal meet) to the outer edge of the weld. A fillet weld is a triangular weld used in joints like T-joints, lap joints, or corner joints.
3. Weld Face
The weld face is the visible surface of the weld after it’s completed. This is the part of the weld that is exposed to the external environment.
4. Groove Weld Size
For groove welds, the size refers to the depth of the groove and the amount of weld material deposited in the joint. Groove welds are typically used in butt joints and can require a full penetration weld depending on the structural requirements.
5. Effective Throat
The effective throat is the theoretical distance that directly affects the strength of the weld. It is often smaller than the actual throat thickness due to various factors like weld defects, penetration, and heat effects.
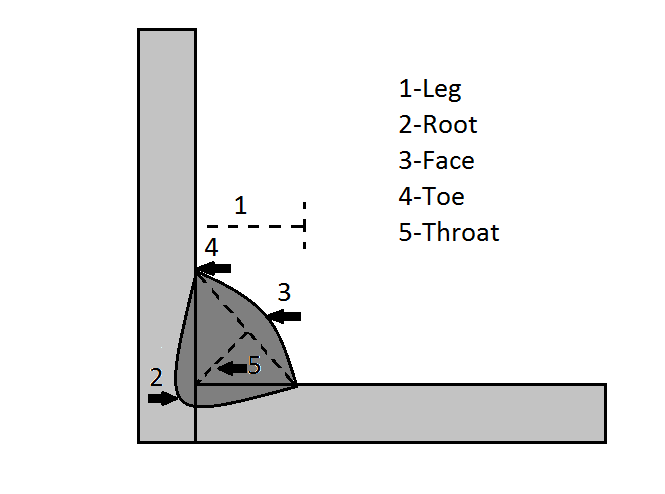
Fillet Weld Measurements
Understanding Weld Sizes and Measurements
Fillet welds are one of the most common types of welds and are measured by their leg size and throat thickness.
1. Leg Size
The leg size of a fillet weld is measured from the root of the weld (where the two metal pieces meet) to the toe (outer edge of the weld). For a fillet weld to meet standard strength requirements, the leg size must be sufficient to handle the loads applied to the joint.
Measurement example: A 6mm fillet weld means each leg of the weld is 6mm in length.
2. Throat Thickness
The throat thickness is a critical factor for determining the strength of the weld, as it measures the shortest distance from the weld root to the weld face. For fillet welds, the throat thickness can be calculated as:
Throat Thickness=Leg Size×0.707\text{Throat Thickness} = \text{Leg Size} \times 0.707Throat Thickness=Leg Size×0.707
This formula applies to equal leg fillet welds (where both legs are the same size). If the leg sizes differ, other calculations may be required.
Example: For a 6mm leg size fillet weld, the throat thickness would be 6mm × 0.707 = 4.24mm.
Tip: The strength of the fillet weld is directly proportional to its throat thickness. Ensuring accurate measurements here is crucial to avoiding under-welding (which weakens the structure) or over-welding (which wastes material and time).
Groove Weld Measurements
Groove welds are typically used in butt joints where the edges of two pieces of metal meet. Groove welds are measured by the depth of the groove (known as groove depth) and the size of the weld required to fill that groove.
1. Groove Depth
The depth of the groove is how deep the metal is prepared for welding. This depth is critical, especially in full penetration welds, where the weld must go all the way through the thickness of the metal.
Example: A 10mm thick plate that requires a full penetration weld will need the groove prepared to 10mm.
2. Weld Size
The weld size in groove welds refers to how much weld material is deposited in the joint. For full penetration welds, the weld size must match the thickness of the material, ensuring that the weld fully fills the groove.
Example: A 10mm thick plate would require a weld size of 10mm for full penetration.
Tip: The type of groove preparation (e.g., V-groove, U-groove, J-groove) also impacts the amount of weld material and the overall strength of the weld.

Weld Size Standards
Most welding codes and standards specify minimum and maximum weld sizes for particular joints. For example:
Fillet Weld Minimum Size: This depends on the thickness of the material. Thicker plates will require larger weld sizes.
Groove Weld Requirements: Groove welds often have more strict size requirements due to their application in load-bearing structures. Full penetration is often required in structural steelwork.
Standards like the AWS D1.1 (Structural Welding Code - Steel) or ISO 5817 provide guidelines for minimum acceptable weld sizes based on joint types and materials used.

Common Tools for Measuring Weld Sizes
Accurately measuring weld sizes is important to ensure the weld meets design requirements and standards. Here are a few common tools used to measure weld sizes:
Fillet Weld Gauge: Used to measure the leg size and throat thickness of fillet welds. This tool typically has a series of angled edges corresponding to standard weld sizes (e.g., 3mm, 5mm, 10mm).
Weld Size Gauge: Similar to a fillet weld gauge but used for groove welds, this tool measures the weld’s reinforcement, leg size, and depth.
Digital Caliper: For more precise measurements, a digital caliper can measure weld thickness, throat size, and other dimensions.
Feeler Gauges: These are used to check the fit-up gaps before welding or to check the root gap in a groove weld. Proper gap control is essential to avoid welding defects like lack of fusion or penetration.
Example Weld Size Calculation
Let’s walk through an example to solidify your understanding.
Scenario:
You are working on a T-joint that requires a fillet weld with a 6mm leg size. The project specifies that the throat thickness must be calculated for a balanced weld.
Leg size: 6mm.
Throat thickness (for an equal leg fillet weld): Throat Thickness=6mm×0.707=4.24mm\text{Throat Thickness} = 6mm \times 0.707 = 4.24mmThroat Thickness=6mm×0.707=4.24mm So, the effective throat thickness is 4.24mm.
What if the legs were unequal?
If one leg is longer (say 8mm) and the other is 6mm, you would need to calculate the throat thickness differently. The formula changes slightly, and you would often refer to weld design codes for such specifics.
Importance of Correct Weld Sizing
Correct weld sizing is essential for the strength and longevity of the welded structure. Over-welding increases material and labor costs unnecessarily, while under-welding can lead to joint failure and compromise the structure’s integrity. It's always recommended to follow the appropriate standards and guidelines like AWS D1.1 or ISO 5817 when determining weld sizes.
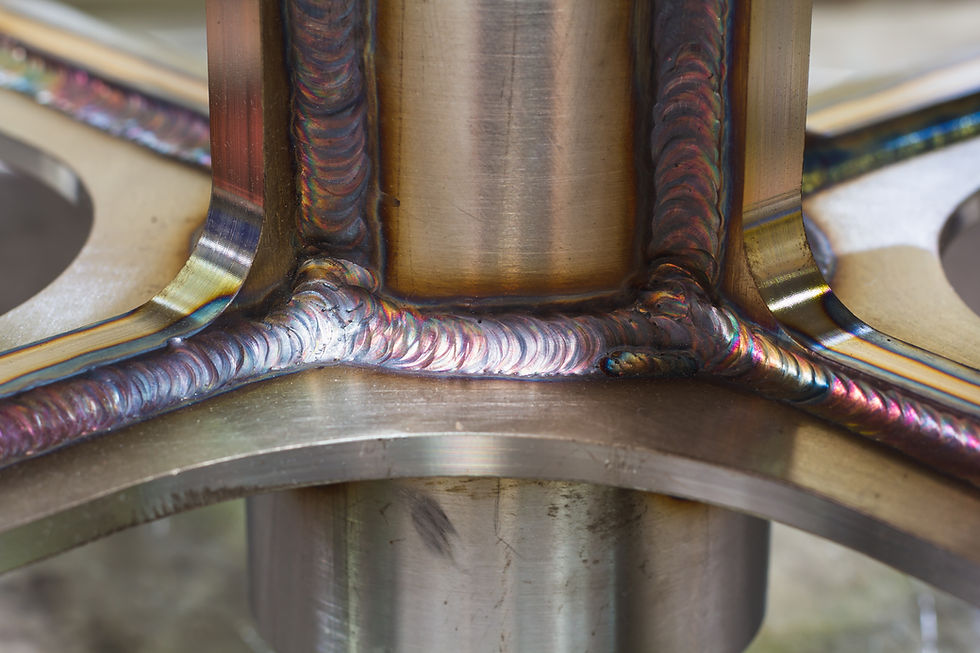
FAQs on Weld Sizes and Measurements
1. Why is throat thickness important in fillet welds? The throat thickness determines the effective strength of the weld. The thicker the throat, the more load the weld can handle. An undersized throat can lead to weak welds, while an oversized throat can result in over-welding and material waste.
2. How is the size of a fillet weld specified in design? In design specifications, fillet welds are often referenced by the leg size. For example, a 6mm fillet weld means both legs are 6mm long.
3. How do I check if a weld meets size requirements? You can use a fillet weld gauge or a digital caliper to measure the leg size, throat thickness, and overall weld size. Ensure these measurements meet the project specifications and applicable standards.
Conclusion
Understanding weld sizes and measurements is critical to ensuring strong, safe, and cost-efficient welds. Whether you're working with fillet welds, groove welds, or any other type, the right weld size directly impacts the structural integrity of your project. Using tools like weld gauges and adhering to standards will help you produce accurate, reliable welds every time.

Comments